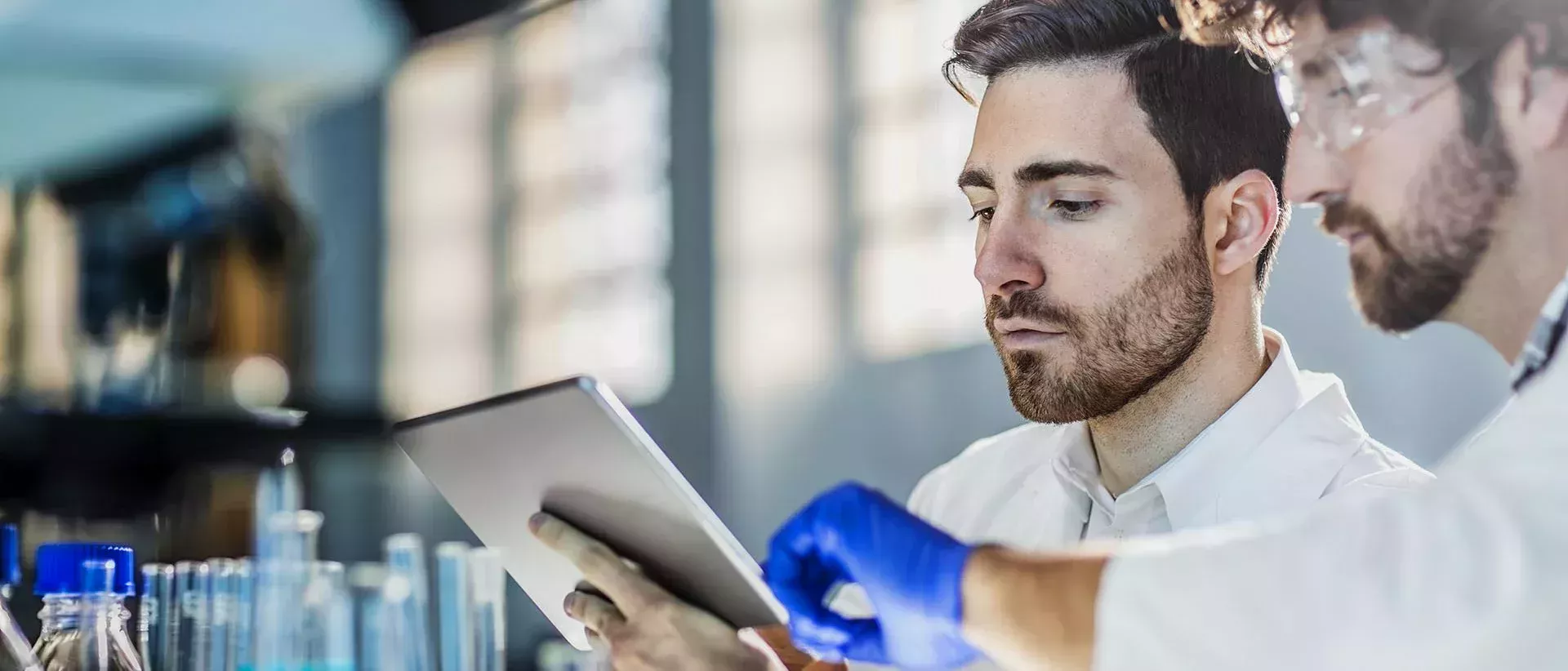
The switch to new drive concepts in the automotive industry as well as other new concepts such as “Industry 4.0”, in which communication between man and machine as well as between machine and machine will play a much bigger role than before, requires new lubricants and lubrication concepts. Automotive developers are increasingly shifting their focus to 48-volt onboard power systems as voltage supplies, as they can power the increasing number of electrical devices in a vehicle with smaller cable cross-sections, component dimensions, and a lower weight. Fully electric vehicles have a voltage of 400 volts or more. Such drive systems, which include electric motors, high-voltage generators, and other vehicle systems, generate considerably more powerful alternating fields than conventional systems or vehicles that do not work with high voltages. The power controllers that control the motor power can cause parasitic stray currents resulting in electric flashovers and send current through anti-friction bearings. The resulting heat can lead to discharge craters, fusion points, melting marks, as well as oxidation and burning of the lubricant grease. This can ultimately destroy the bearing.
These can be countered by electrically insulated anti-friction bearings or a new concept based on lubricating greases with conductive additives. The project “Increase production efficiency based on the online measurement of the electrical properties exhibited by conductive lubricants – PeOMeE” intends to target findings specifically for “Industry 4.0”. This involves a sensor system deployed in the ongoing production process to measure the conductivity of the lubricating grease used in the system, as well as their temperature, wear on the lubricant and wear on the lubricated anti-friction bearing. In addition, continual online state monitoring and optimized state-oriented load regulation will be enabled. In this project, BECHEM is entrusted with the development of the specialty lubricant and its adaptation to the sensor system. Other partners in the project funded by the European Regional Development Fund include Eich Rollenlager GmbH, Hattingen (anti-friction bearings), Triboot Technologies GmbH, Mülheim a. d. Ruhr (IT, software), Turck duotec GmbH, Halver (sensors), the Fachhochschule Südwestfalen, and 4Inno Ingenieurgesellschaft mbH & Co. KG, Olpe (development of electronics).
Funding reference: EFRE-0800788/798/799/800/801/(802)