Steel IndustryWhen things get hot
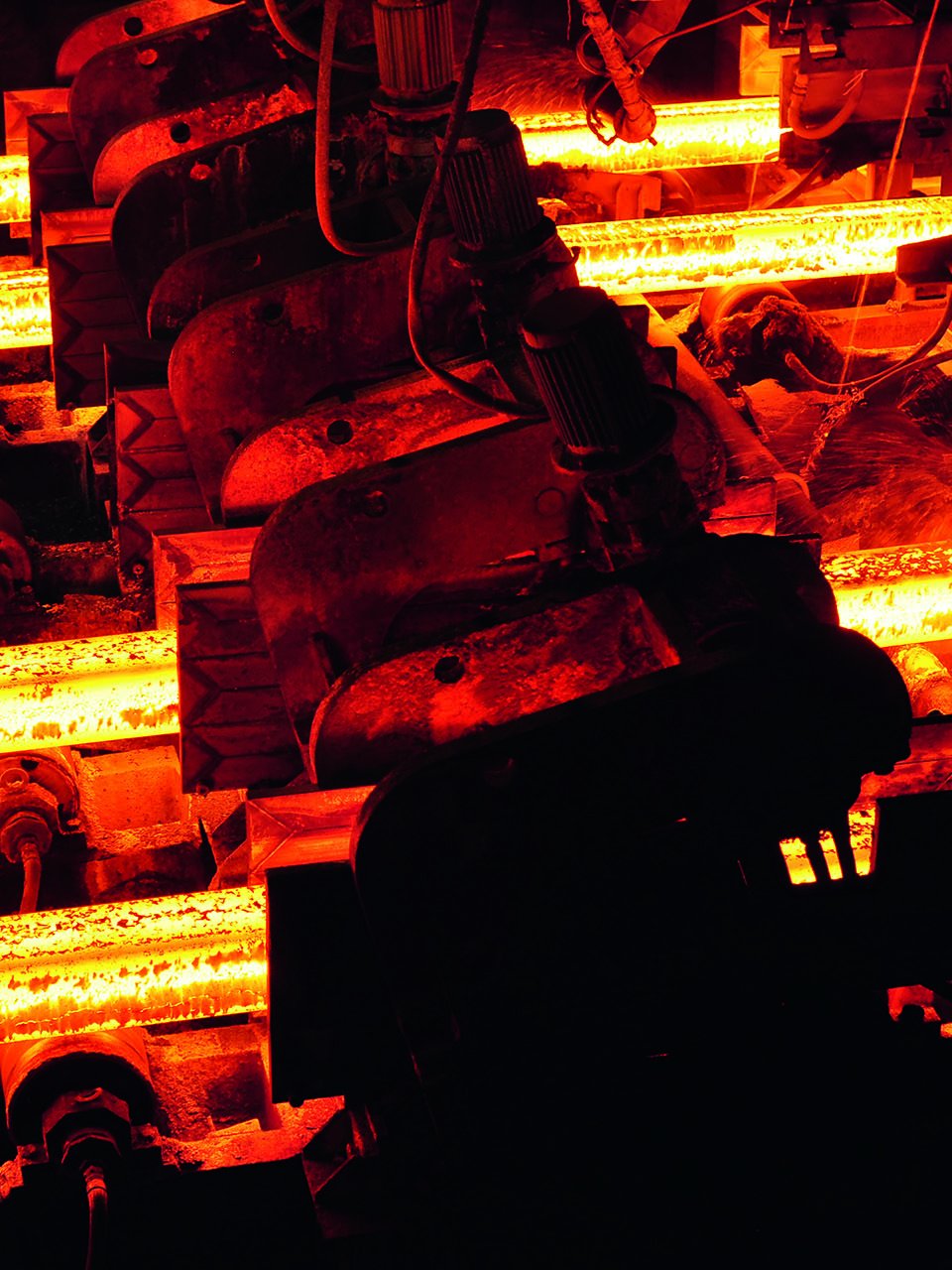

The demand on lubricants is also increasing with the requirements for the technical equipment in the steel industry. The targeted use of BECHEM high performance lubricants can reduce costs, protect the environment, and reduce the strain on machines.
The steelmaking process is defined by difficult tribological framework conditions, such as process temperatures, corrosive coolants, abrasive dusts, or large shock loads. BECHEM lubricants offer sophisticated solutions for a trouble-free production process. They make a great contribution to protecting surfaces from tribocorrosion and to minimizing foreign particle entry.
BECHEM has developed lubricants with outstanding water and temperature resistance as well as very good corrosion protection for high performance operation in the steel industry. Many products are the result of an intensive research cooperation with leading steel producers in which renowned machine and system manufacturers as well as companies from drive technology were involved.
BECHEM products make a considerable contribution to the avoidance of production downtimes and to extending the technical service life of equipment.
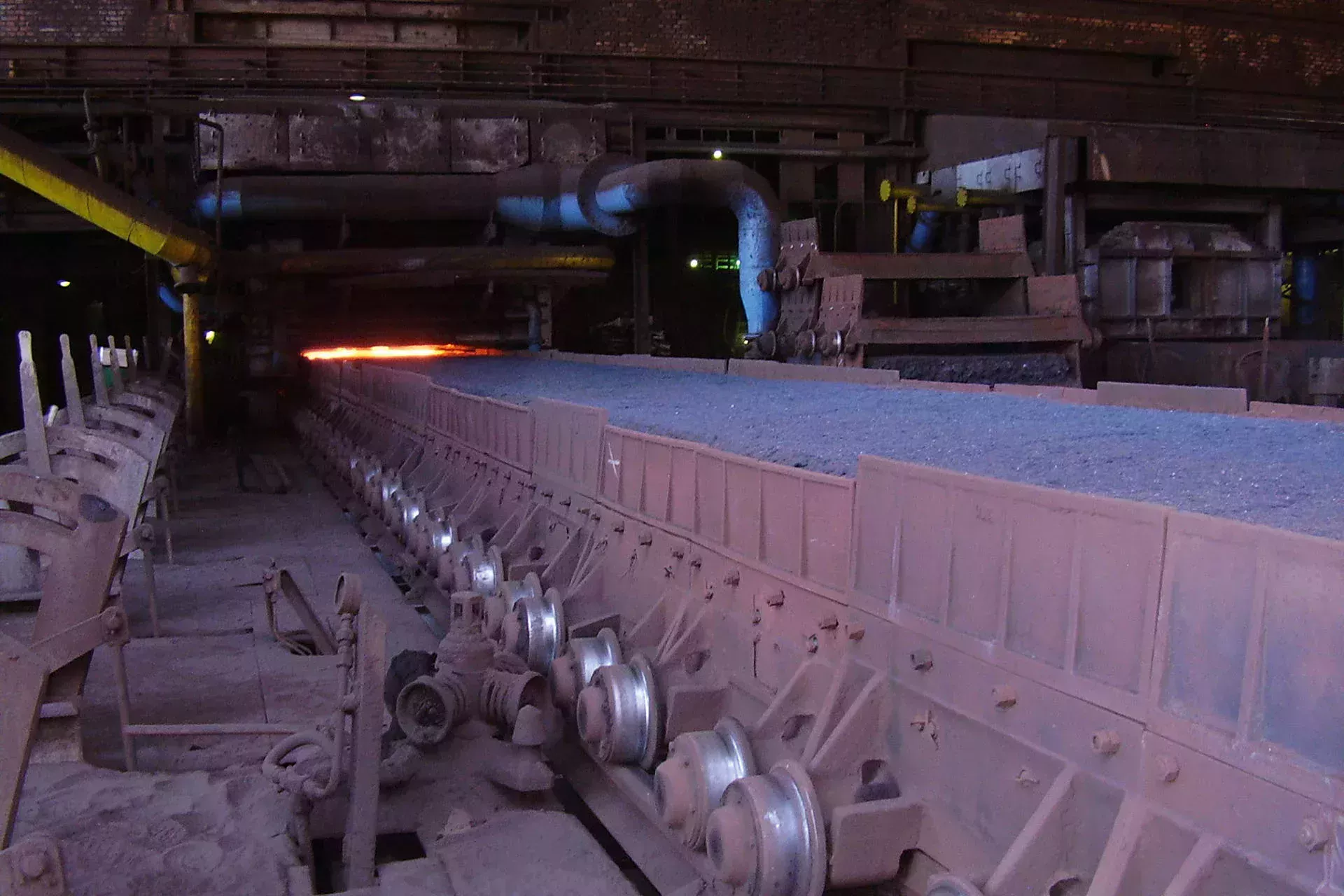
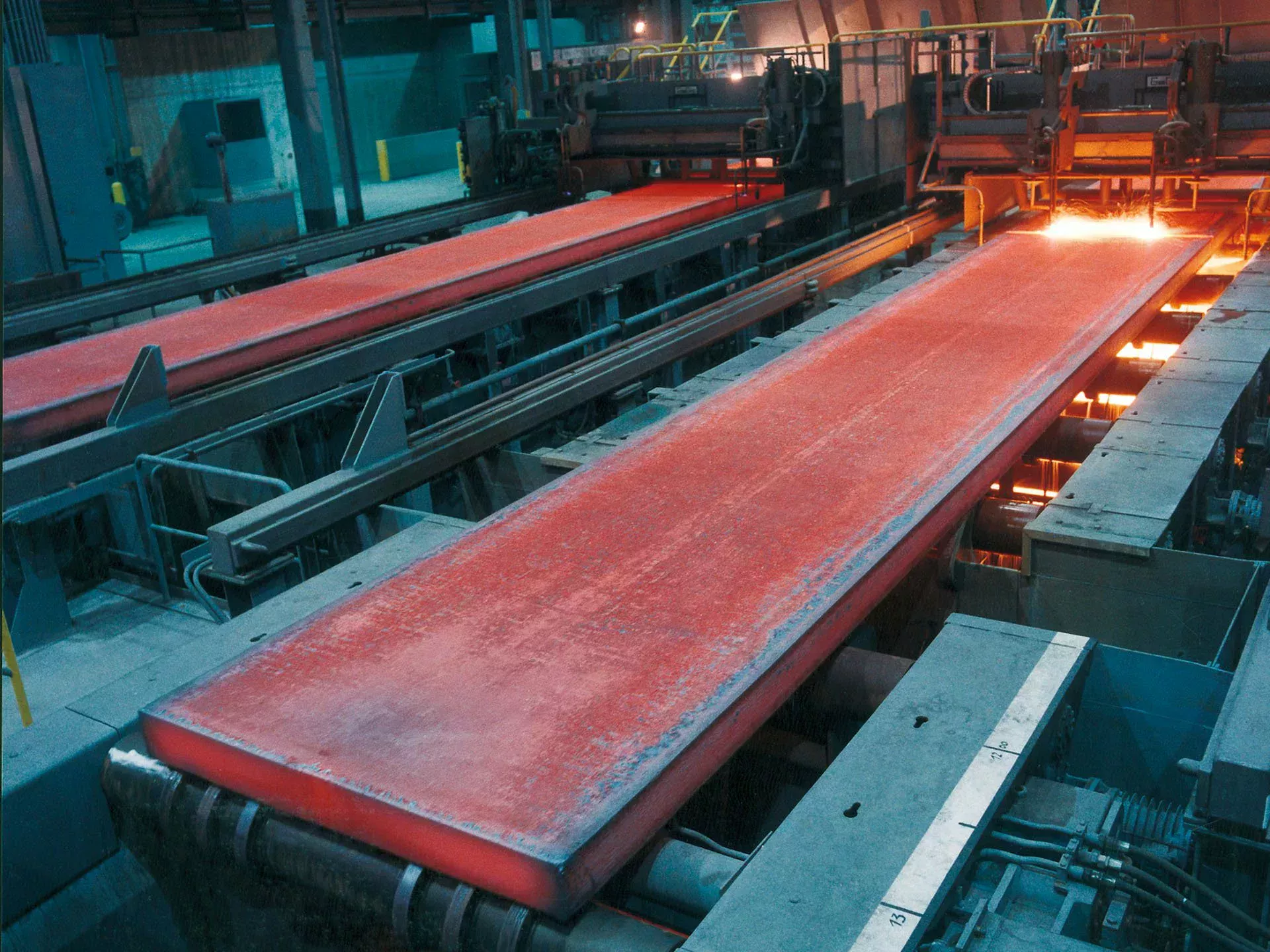
Berutemp M 21 HT has proven itself worldwide in the continuous casting line
The operating conditions in a continuous casting line are characterized by low speeds, high thermal stress, and corrosive process water ingress. For system-critical applications in steelworks, such as the ladle turret, strand guiding rollers or converter bearings, BECHEM special lubricants were developed in various qualities, which, for example, differ through the addition of solid lubricant particles or the base oil viscosity.
Central lubricants for the bearings of guide rollers are a tribologically demanding challenge. Contradictory challenges need to be met, such as the good transportability in central lubrication systems with a simultaneously high base oil viscosity for lubricating bearings at slow speeds. In addition, the requirements in the continuous casting lines of the steelworks differ from each other considerably. For this broad range of applications, BECHEM offers a variety of proven lubrication greases, such as Berutemp M 21 HT, Berutox M 21 KN, BECHEM Ceritol PSA 12 H, BECHEM High-Lub LT 2 EP, Beruplex Alutherm 2, Beruplex CS 2 EP, or Beruplex HTA. Synthetic oils are ideal for oil-air lubrication systems.
The flame-retardant and water-miscible BECHEM Starlit EM-MA-DF is used in the hydraulic system of the electric arc furnace. The side bearings of the converter, which are a particularly sensitive lubrication point, are reliably supplied with the heavy load lubrication greases BECHEM High-Lub FA 40 MO, BECHEM High-Lub FA 50 MO, or the newly developed BECHEM High-Lub FA 50 MO 1 for an even longer service life. BECHEM High-Lub FA 50 MO for the bearings of the ladle turret and Berulit GA-series for the open drives have proven themselves for efficient lubrication.
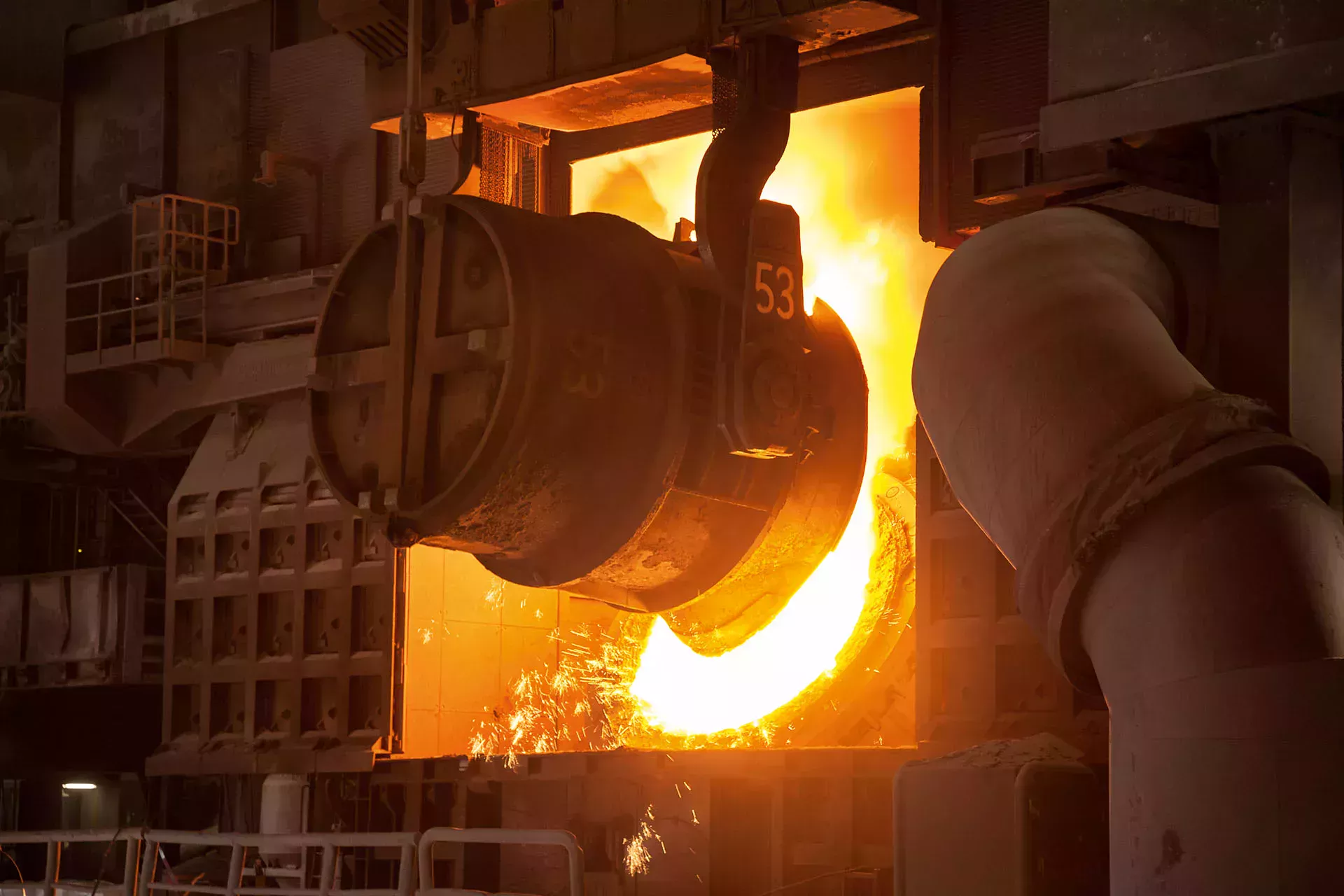
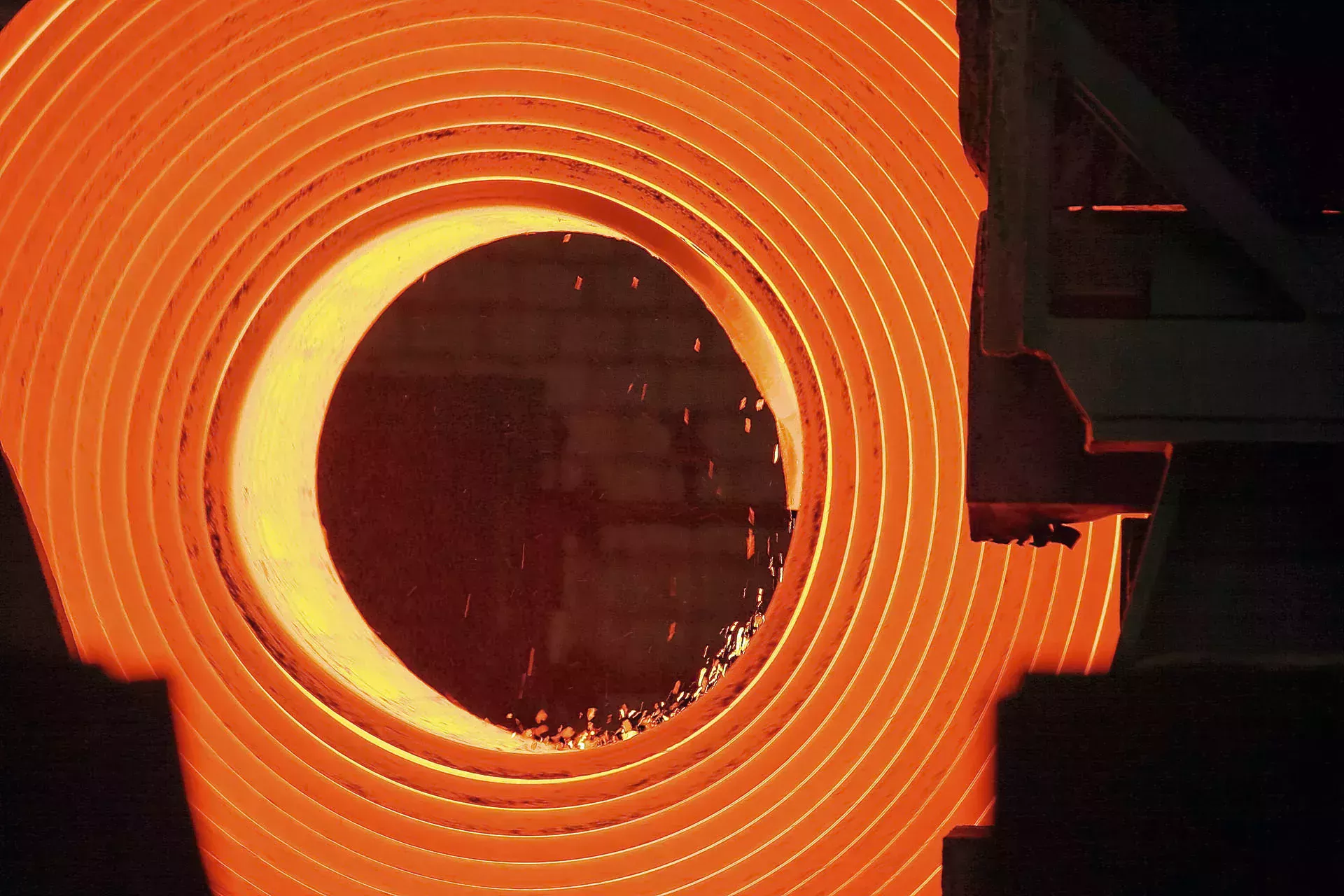
Occasionally, higher speeds and shock loads occur in hot strip, cold strip, heavy plate, and section mills. For the hot rolling process, the lubrication must have a good resistance to high temperatures and process water. In the cold rolling mill, the product must also be resistant to a chemically active rolling mill emulsion. Thanks to the good wear protection and excellent sealing and corrosion protection, tailor-made BECHEM lubricants optimize the performance and operating time of the system.
BECHEM High-Lub 67-400 KS was developed together with the German steel industry, bearing manufacturers, and universities for the challenging applications in work roller bearings of rolling mills and is used in bearings for an operating period of one year without the need for any relubrication. BECHEM High-Lub FA 50 is successfully being used around the world for roughing stands and slab upsetting presses. The central lubrication of the mill roller tables and peripheral system parts is provided by BECHEM High-Lub LT 2 EP or Beruplex CS 2 EP, since these products have good transportability and versatile lubrication properties. BECHEM Ceritol PSA 12 H has proven itself for the special requirements of the reeling machine.
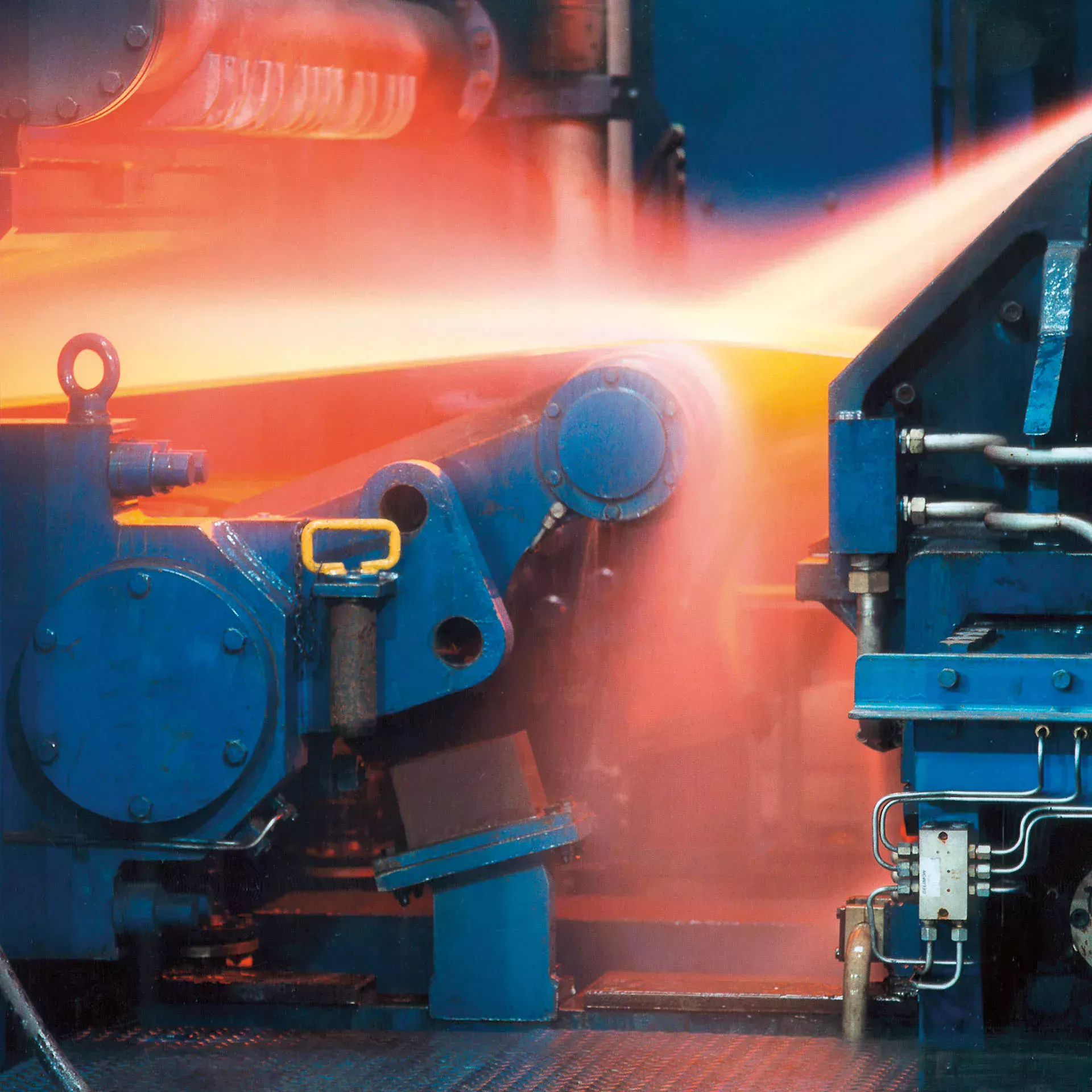
In cold rolling mills, the systems are run at significantly higher speeds. The demands on the lubricant to ensure that the system runs flawlessly are very high. Since a chemically active roller emulsion is used in many cases, chemical resistance and high sealing performance are crucial. There is a direct risk of overheating due to the increased hydrodynamic losses from higher operating speeds. The viscosity and composition of the lubricant must therefore be adapted in terms of the temperature increase and the minimization of the premature lubrication degradation.
The supporting roller bearings are lubricated with BECHEM Ovitol KT 460 VA. Despite the water ingress, the oil ensures hydrodynamic lubrication, as it quickly separates from the water and the oil film is not affected. To lubricate the oil flow bearing of the supporting roller, BECHEM offers a unique system in which the high performance circulating oil is matched to the process water in each roller mill and is adjusted for each reappointment. This exclusive technology was developed in cooperation with major steel producers and a leading plant engineering company.

The many different operations of a metallurgical plant are marked by complex production processes that pose a variety of technical lubrication tasks. BECHEM offers an extensive lubrication range for this, which covers these tasks. In addition to lubrication greases for general and special applications, it also includes hydraulic fluids, cooling lubricants, corrosion protection media, cable lubricants and chain oils.
Mineral oil-based and synthetic lubricating oils are available for gears and oil circulation. The mineral oil-based oils of the BECHEM Staroil G series reliably cover a whole range of applications. Synthetic oils are recommended in the case of special conditions, such as elevated temperatures, larger loads, previously damaged drives, or longer oil change intervals. Here the poly-alpha-olefins of the Berusynth HC series or the polyglycols of the Berusynth EP series have established themselves worldwide.
BECHEM offers comprehensive technical service through a globally available team of highly qualified application engineers. This may include the following items according to the respective agreements:
Service Package
- Technical inspections
- Lubricant management and consultation
- Sampling and analysis of lubricant samples
- Creation of lubrication charts determining the monitoring or failure criteria
- Custom development of lubricants
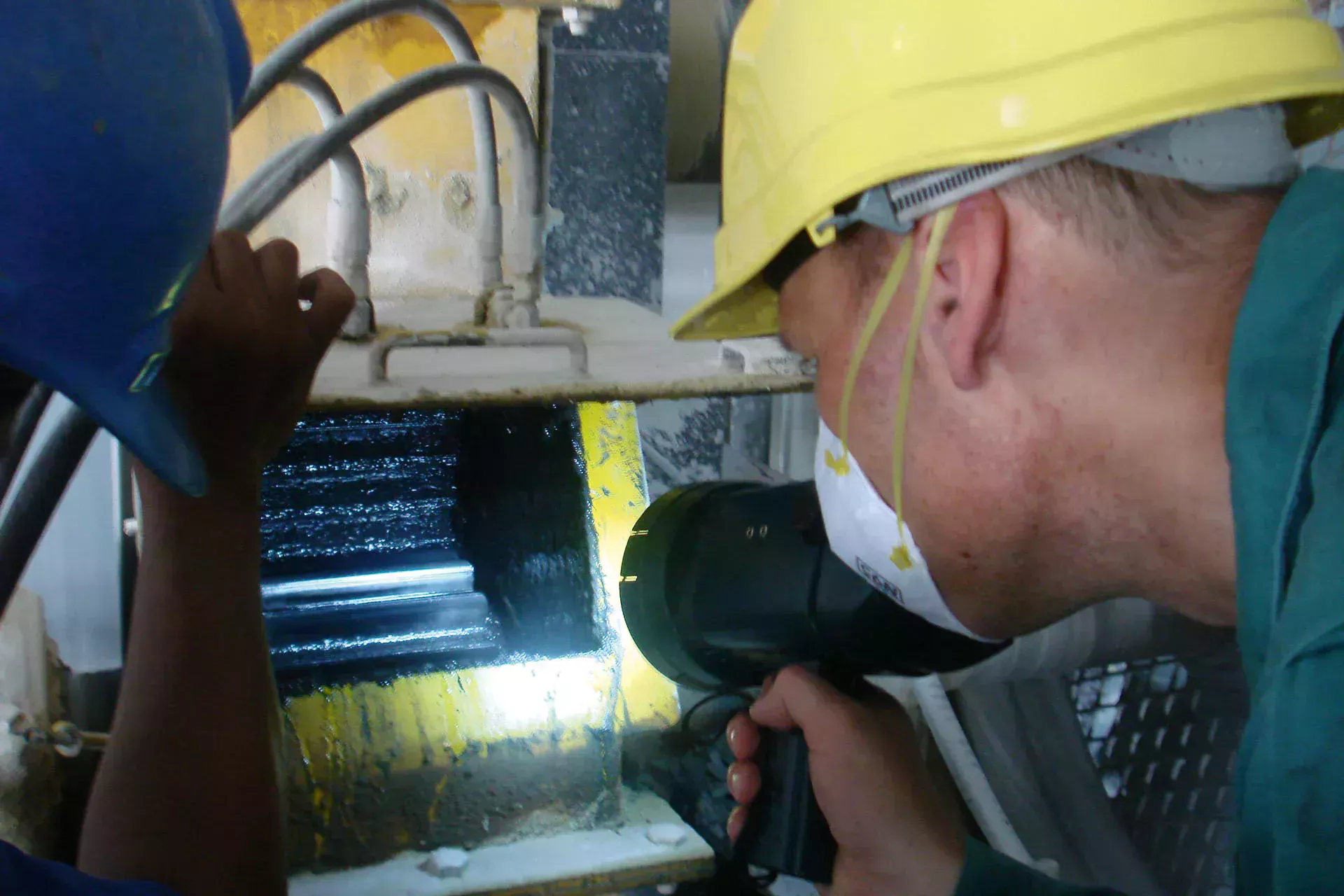
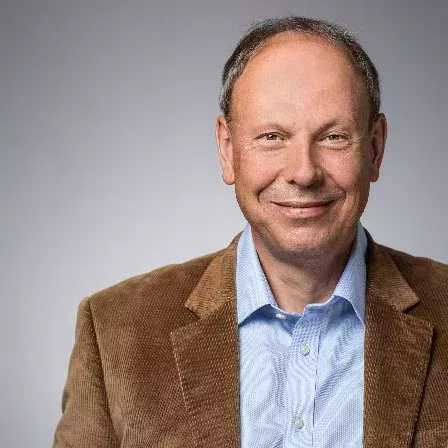
Global Market Manager Steel
BECHEM expert for:
- Continuous casting
- Rolling
- Special applications
BECHEM Complex CM 21Innovative long-term lubricating grease with outstanding water resistance
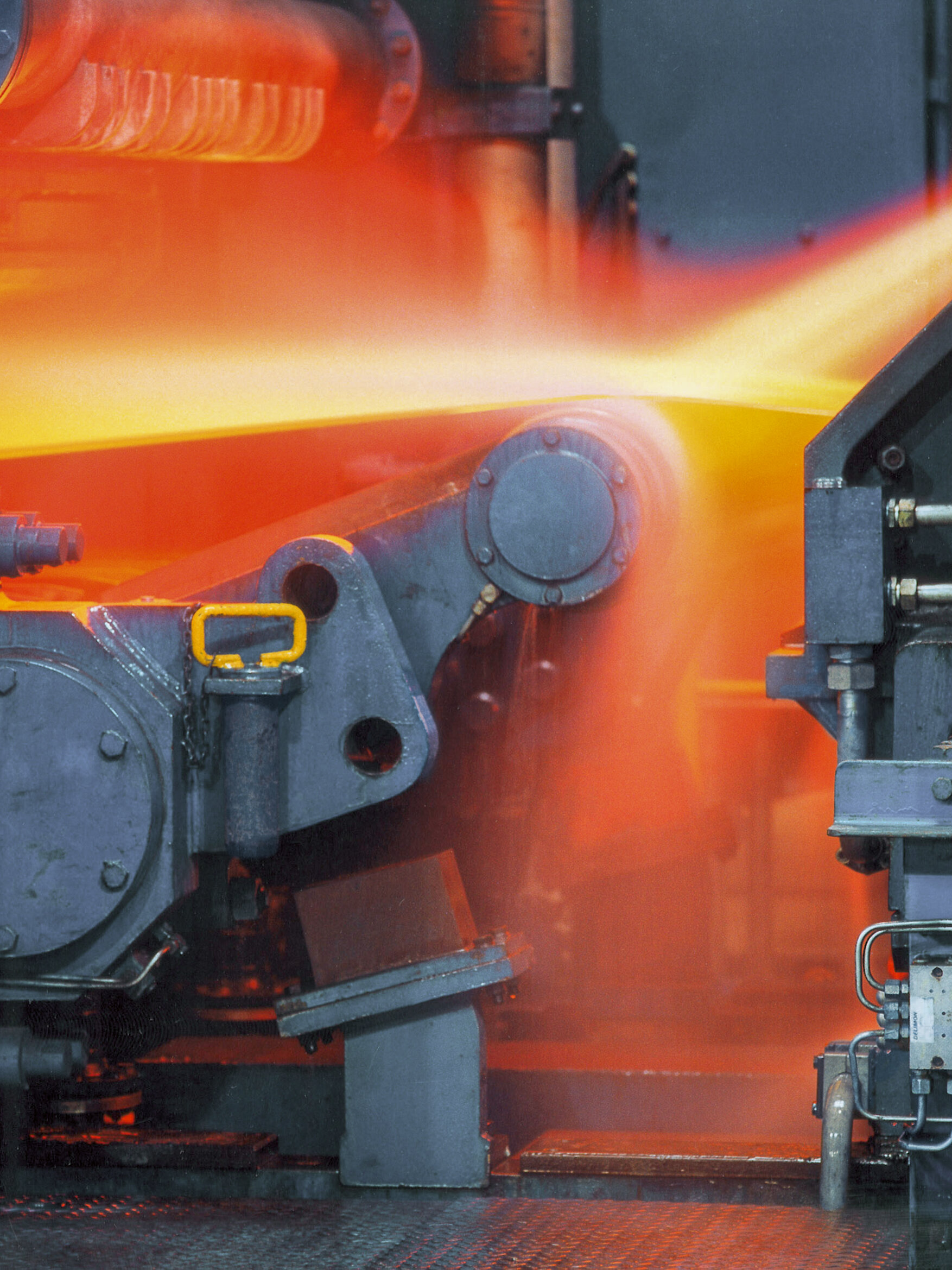
Lubrication solutions for the steel industry
